Gravity Compensation for 6-RSS Parallel Robot
In this study, a novel decoupled inverse dynamic model of a 6-RSS parallel manipulator is proposed using the Force Distribution algorithm. Unlike previous models, this model takes into account the changing forces exerted on the cranks by the moving platform and rods, which vary depending on the position of the moving platform. The model is formally decoupled, as each limb can be modeled separately, but it is still coupled due to the latent influence of the motion and other parts of the manipulator. The static equilibrium equations were derived to obtain reaction forces, and QR factorization was used to obtain a suboptimal solution. This approach has not been previously used in parallel manipulators of this type, making it a significant contribution to the field.
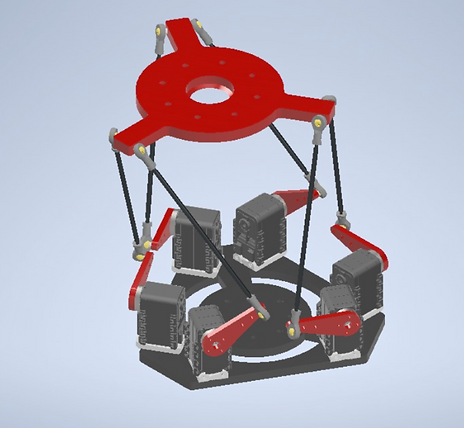.png)
System description
The paper discusses a mechanism that has the ability to produce complete spatial movement with 6 degrees of freedom, as described in Equation (1). This movement comprises 3 degrees of freedom for position and 3 degrees of freedom for orientation.
To enable this 6-DOF motion, the mechanism employs six servo motors that operate the moving platform. Each servo motor controls an arm, consisting of a crank and a rod connected by a passive spherical joint. The rod is then attached to the moving platform through another passive spherical joint.
These arms create an RSS (Revolute-Spherical-Spherical) kinematic chain, where the active or servo motor-actuated joint is the revolute joint that connects to the base platform. All six arms work together to create the desired movement.
Figure 1:Physical structure of the 6 RSS parallel platform
Methodology and Joint Torque Calculation
There are six equations in this set, each with 18 unknowns. As a result, it lacks a singular solution. The QR factorization, is used to solve this underdetermined problem and obtain the minimum-norm solution.
We propose a novel decoupled inverse dynamic model with uneven mass distribution of the moving platform and rods on the cranks employing the Force Distribution algorithm. We call the first model as ‘decoupled inverse dynamic model’ in the sense that each limb can be modeled separately such that six motor-crank models are obtained for the six limbs. It is worth noting that this model is still coupled in fact but it is formally decoupled, since the influence of the motion and the rest of the manipulator is latent in the forces exerted on the cranks by the other moving parts of the manipulator (the moving platform and the corresponding rod)
Results
The output from the Matlab code was successfully verified in dynamic simulation on the 3-D model of the 6-RSS parallel robot in Inventor. The robot balanced itself keeping a stable configuration under the influence of gravity.
Figure 2: Robot stabilizing in both symmetric and unsymmetric positions.
Discussion
There are several approaches for gravity compensation like gravity compensation by counterweights mounted on the links of the initial system, gravity compensation by counterweights mounted on the auxiliary linkage connected with the initial systems, gravity compensation by springs, gravity compensation with auxiliary actuators.
Apart from the decoupled inverse dynamic model approach lagrangian inverse dynamic model method can also be used to find out the joint torques. The difference between the two models is in the gravity vector that expresses the coupling between the limbs and the nonlinearity of the model.

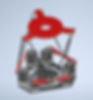
